Leads and Extensions are manufactured by Helical Anchors Inc. Expect the best quality product among the helical industry.
Helical Extensions
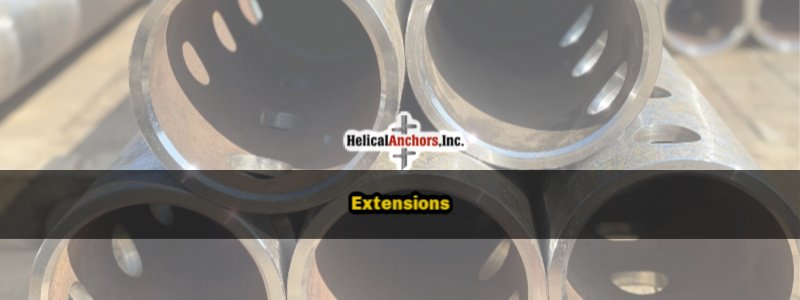
Helical Anchors Inc manufactures the strongest extensions in the helical industry. It’s a simple product but plays an essential role in the anatomy of a helical pile system. Its purpose is to extend the steel to the required depth so the lead can anchor to the proper strata. In short the process includes the lead being carefully installed in the desired location. Once embedded into the soil an extension is attached to the lead and to the drive motor. Torque is again applied to further advance the lead into the ground.
Extensions continue to be added until the required depth or required torque is achieved.
All extensions from all of the manufacturers do the same thing and consists of both a male and female tool joint with a mid-body shaft, the important thing is how these three pieces of steel are connected.
Helical Anchors Inc uses a process called inertia welding. It is a patented process that takes two different pieces of steel and by applying rotary and pressure conjoins them. This process is hands down the best method to weld two pieces of steel together. There are no added metals, no human error, and no special skill requirements. By rotating and pressing the two metals together we generate enough friction to generate enough heat to forge the two metals as one.
Inertia welding allows us to manufacture the strongest helical anchor in the world.
Helical Leads
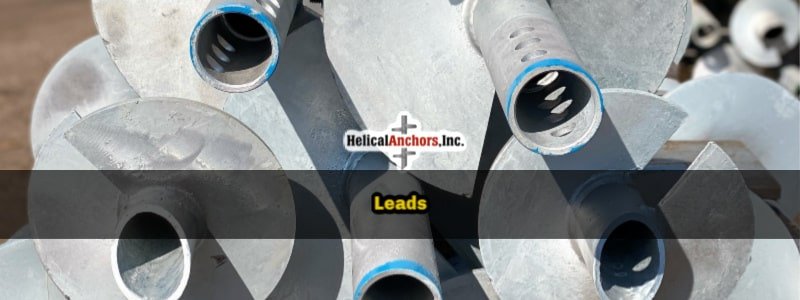
Leads section is constructed of a tip, helixes, and a connection. It is what pulls the helical anchor into the ground. It does this the same way a wood screw is screwed into the wood. The pitch of the flight(s) pulls the anchor into the ground.
Helical Anchors Inc manufactures their leads sections with 80 KSI steel tubing and 107 KSI box connections. The flights are plasma cut in the house out of grade 50 plate and formed by a die to ensure precise pitch requirements. All flights are hand-measured to guarantee 100% compliance with the designated tolerances.
We have many ICC certified products so maintaining these tolerances are imperative. All flights are welded by a certified D1.1 welder. They are strategically welded in place to ensure minimal soil disturbance as they are pulling the helical piles through the soil.
With a 3” pitch on the flight(s) and a steady installation rate of 3” per rotation the maximum amount of skin friction can be achieved. The more skin friction generated the quicker the installer will achieve the desired torque.
If the pitch of the flight is 6” the installation rate is increased to 6” per rotation. Increasing the helix pitch does a few things; it is typically done on larger piles to help with installation speed, it also adds pull-down strength to help ease installation.