Discover how helical anchors evolved from Alexander Mitchell’s 19th-century invention to today’s sophisticated engineering solutions powering sustainable construction and renewable energy infrastructure.
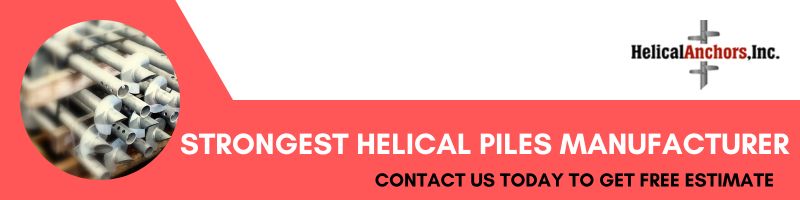
Introduction
Few engineering innovations have transformed foundation technology as quietly yet profoundly as helical anchors. These ingenious devices—also known as screw piles, helical piers, or helical foundations—have revolutionized how we secure structures to the earth. From their humble maritime beginnings to cutting-edge applications in renewable energy, the evolution of helical anchors represents a fascinating journey through engineering history. This article traces their development from conception to the present day, highlighting the technological advancements that have made them indispensable in modern construction.
The Genesis of an Innovation: Alexander Mitchell’s Maritime Breakthrough
The story of helical anchors begins in the early 1830s with Irish engineer Alexander Mitchell, a remarkable figure who overcame significant personal challenges to create lasting engineering solutions. Having gone completely blind at age 21 following complications from smallpox as a child, Mitchell channeled his understanding of mechanics and mathematics into solving one of the era’s most pressing maritime challenges.
After retiring from his brick-making business in 1832, Mitchell patented the screw pile in 1833, driven by the urgent need for reliable lighthouse foundations in challenging marine environments. Unlike traditional piles that relied solely on friction against the soil, Mitchell’s invention utilized a screw-like mechanism with helical flanges to provide exceptional holding capacity in shifting soils.
The motivation behind Mitchell’s innovation was both practical and humanitarian. As maritime commerce expanded rapidly during the Industrial Revolution, there was an urgent need for reliable lighthouses in challenging locations. Conventional foundation methods often failed in sandy or muddy seabeds, leading to tragic consequences for shipping and the loss of countless lives at sea.
First Success and Validation
In 1838, Mitchell’s innovation found its first major application at the Maplin Sands lighthouse in the Thames Estuary, England. The success was immediate and remarkable. While construction began in 1838, the lighthouse was first lit in 1841, demonstrating the superior load-bearing capacity of helical foundations in unstable soils where previous attempts had failed.
This pioneering project involved 20-foot-long piles with cast iron screws 4 feet in diameter at the bottom, which were screwed into the sand by hand with a team of men turning a capstan. The lighthouse stood firmly where conventional approaches had proven inadequate, establishing the credibility of helical foundation technology.
Rapid Expansion Across Maritime Applications
Following the success at Maplin Sands, helical pile technology quickly spread throughout the British Empire and beyond. Mitchell’s design was employed at Fleetwood in Morecambe Bay in 1839 and in Belfast Lough in 1844, with the concept rapidly gaining acceptance among marine engineers.
Between 1840 and 1870, over 100 screw-pile lighthouses were constructed worldwide, including notable examples in:
- The Chesapeake Bay (United States)
- Ireland’s extensive coastline
- Colonial India’s major ports
- Australian harbors and waterways
Beyond lighthouses, engineers began adapting Mitchell’s invention for various maritime structures:
Pier Supports: The rapid installation capability in tidal zones made helical piles ideal for structures like Southend Pier in England, where traditional construction methods would have been prohibitively complex.
Harbor Moorings: The superior holding capacity in sandy bottoms proved invaluable for major ports like Liverpool, where secure anchoring was essential for commercial operations.
Bridge Foundations: The stability provided in riverbed sediments supported critical infrastructure projects, including early applications in railway bridge supports like those used in the Tay Rail Bridge project.
The versatility of helical foundations became increasingly apparent as engineers discovered their effectiveness across different soil conditions and structural requirements, setting the stage for broader applications beyond maritime use.
Transition to Terrestrial Engineering
As the Industrial Revolution transformed society, helical anchor technology naturally evolved from maritime applications to land-based construction. This transition was driven by several converging factors that created new demands for rapid, reliable foundation systems.
Railway Expansion: The explosive growth of railway networks created unprecedented demand for quickly installed, reliable foundation systems. Railway bridges, platforms, and signal structures required foundations that could be installed rapidly without disrupting existing operations or requiring extensive excavation in varied terrain.
Urban Development Pressures: As cities grew vertically and expanded outward, engineers needed foundation solutions for increasingly heavy structures on varied soil conditions. Traditional foundation methods often proved inadequate for the pace of urban development or the diverse soil conditions encountered in expanding metropolitan areas.
Manufacturing Revolution: Advances in metallurgy and precision machining enabled more sophisticated fabrication of helical components. The transition from hand-forged components to machine-manufactured parts improved consistency, strength, and installation reliability.
During this transformative period, helical anchors began evolving from their original maritime design. Engineers experimented systematically with various helix configurations, shaft materials, and installation techniques. By the early 1900s, specialized equipment for installing helical foundations on land had emerged, making the technology more accessible to general construction contractors and expanding its potential applications significantly.
Scientific Understanding and Material Innovation
The period between 1920 and 1960 marked a crucial phase in helical anchor development, characterized by more rigorous scientific understanding of soil mechanics and significant material improvements that transformed the technology from an empirical art to an engineering science.
The Foundation of Soil Mechanics
The emerging field of soil mechanics, pioneered by Karl Terzaghi and other luminaries, provided a theoretical framework for understanding how helical anchors functioned in different soil conditions. This scientific approach enabled engineers to:
- Develop mathematical models for predicting load capacity based on soil properties
- Understand the critical relationship between installation torque and ultimate holding capacity
- Document and predict the behavior of helical anchors under different loading conditions (compression, tension, and lateral forces)
- Establish design methodologies that could be applied consistently across projects
Material Science Breakthroughs
Parallel advancements in materials science dramatically improved helical anchor performance and reliability:
Advanced Steel Alloys: High-strength steel alloys replaced cast iron, offering superior tensile strength, improved resistance to bending, and better fatigue characteristics under cyclic loading conditions.
Corrosion Protection: The development of hot-dip galvanization and advanced protective coatings extended service life by combating corrosion, particularly in marine and aggressive soil environments.
Manufacturing Standards: Standardized manufacturing processes improved quality control and reliability, reducing field failures and increasing confidence in design predictions.
These developments transformed helical anchors from specialized maritime technology to versatile foundation elements suitable for diverse applications across multiple industries and soil conditions.
The Era of Industrialization and Standardization
The decades between 1960 and 1990 witnessed the true industrialization of helical anchor technology, as several critical developments converged to create a mature, standardized industry capable of supporting large-scale applications.
Hydraulic Installation Revolution
The development of hydraulic torque motors and specialized installation equipment transformed the helical anchor industry fundamentally:
Enhanced Precision: Hydraulic systems provided precise torque control, enabling accurate installation to design specifications and improving quality assurance.
Increased Efficiency: Mechanized installation dramatically reduced installation time and labor requirements, making helical anchors economically competitive with traditional foundation methods.
Access Capabilities: Compact hydraulic equipment enabled installation in limited-access areas where conventional foundation methods would be impractical or impossible.
Quality Control: Measurable torque readings provided real-time verification of installation quality and capacity, introducing scientific rigor to the installation process.
Depth Capabilities: Powerful hydraulic systems allowed for deeper installations in challenging soil conditions, expanding the range of suitable applications.
Industry Standardization and Testing Protocols
As applications diversified, industry standardization became essential for widespread adoption:
Testing Protocols: Comprehensive testing procedures were established to verify capacity and performance under various loading conditions, creating confidence among engineers and building officials.
Design Standards: Industry-specific design standards emerged for different applications, providing engineers with reliable design methodologies and safety factors.
Certification Requirements: Installer certification programs ensured proper installation techniques, reducing field failures and improving overall industry reputation.
Load Testing Procedures: Standardized load testing procedures verified in-field performance, bridging the gap between theoretical design and actual capacity.
Expanding Commercial Applications
During this period, helical anchors found widespread adoption in numerous commercial applications:
Transmission Infrastructure: Utility companies embraced helical anchors for transmission tower foundations, appreciating their resistance to uplift forces and rapid installation capabilities.
Pipeline Systems: Oil and gas companies utilized helical anchor systems for pipeline anchoring, particularly in areas subject to soil movement or buoyancy forces.
Retaining Structures: Civil engineers incorporated helical anchors as tiebacks for retaining walls, providing reliable tension capacity in constrained urban environments.
Structural Underpinning: The ability to install helical anchors with minimal vibration made them ideal for underpinning existing structures without causing damage.
Highway Infrastructure: Transportation departments adopted helical anchors for highway sign foundations, guardrail systems, and other roadside infrastructure requiring rapid installation with minimal traffic disruption.
The Digital Revolution and Precision Engineering
The digital revolution of the 1990s and 2000s dramatically impacted helical anchor technology, introducing unprecedented precision in design, manufacturing, and installation processes.
Computer-Aided Design and Analysis
Advanced software tools transformed how helical anchors were designed and analyzed:
Finite Element Analysis: Sophisticated modeling capabilities enabled precise stress analysis and optimization of helix geometry, shaft dimensions, and connection details.
Soil-Structure Interaction: Complex soil-structure interaction could be simulated before installation, allowing engineers to optimize designs for specific site conditions and loading scenarios.
Custom Design Capabilities: Engineering software enabled rapid development of custom configurations for specific applications, expanding the versatility of helical anchor systems.
Load Capacity Prediction: Advanced analysis tools provided more accurate prediction of load capacity, reducing the need for extensive field testing and improving design efficiency.
Manufacturing Precision and Quality Control
Computer-controlled manufacturing processes revolutionized production quality and consistency:
CNC Machining: Computer numerical control (CNC) machining ensured precise helix geometry and shaft dimensions, improving installation performance and load capacity predictability.
Automated Welding: Robotic welding systems improved connection integrity and consistency, reducing quality variations and improving long-term reliability.
Quality Assurance Systems: Integrated quality control systems reduced manufacturing defects and provided comprehensive documentation of product specifications.
Mass Customization: Flexible manufacturing systems enabled efficient production of custom designs, supporting specialized applications without sacrificing economies of scale.
Advanced Installation Monitoring
Digital technology transformed the installation process, introducing unprecedented quality control and verification capabilities:
Real-Time Monitoring: Advanced torque monitoring systems verified design assumptions during installation, providing immediate feedback on soil conditions and anchor performance.
GPS-Guided Installation: Precision positioning systems improved placement accuracy, particularly important for large projects with strict tolerance requirements.
Digital Documentation: Comprehensive digital records provided quality assurance documentation and facilitated long-term performance monitoring.
Remote Oversight: Digital communication systems allowed expert oversight of installation operations at remote or challenging sites, improving quality control and reducing project risks.
Contemporary Innovations and Sustainable Solutions
In recent years, helical anchor technology has continued evolving, with particular emphasis on sustainability, environmental responsibility, and integration with other advanced technologies to meet the challenges of modern construction and infrastructure development.
Environmental Advantages and Sustainable Construction
The environmental benefits of helical anchors have gained increasing recognition as the construction industry prioritizes sustainability:
Minimal Site Disturbance: Helical anchor installation requires significantly less excavation and site disturbance compared to conventional concrete foundations, preserving existing ecosystems and reducing restoration requirements.
Carbon Footprint Reduction: Studies indicate that helical anchor systems can reduce carbon footprint by up to 80% compared to equivalent concrete foundations, primarily due to eliminated concrete production and reduced transportation requirements.
Recyclable Components: Steel components can be completely recovered and recycled at the end of their service life, supporting circular economy principles and reducing waste.
Chemical-Free Installation: Unlike concrete foundations, helical anchors require no curing time or chemical processes, eliminating potential soil and groundwater contamination.
Reversible Installation: The ability to completely remove helical anchors makes them ideal for temporary structures or environmentally sensitive areas where permanent ground disturbance must be minimized.
Renewable Energy Infrastructure Support
The renewable energy sector has enthusiastically embraced helical anchor technology, driven by the need for rapid deployment and minimal environmental impact:
Solar Array Foundations: Large-scale solar installations utilize thousands of helical anchors, achieving 35% reduction in installation timelines compared to concrete foundations while minimizing site preparation requirements.
Wind Turbine Support: Helical anchor systems provide adjustable foundation solutions for varied soil conditions, enabling wind farm development in previously challenging locations and reducing site preparation costs.
Floating Solar Anchoring: Innovative applications in floating solar installations provide secure anchoring with minimal environmental impact, expanding viable locations for solar deployment.
Transmission Infrastructure: Reliable support systems for remote transmission lines accelerate grid connections for renewable energy projects, supporting the expansion of clean energy infrastructure.
Smart Technology Integration and Industry 4.0
The latest generation of helical anchors incorporates smart technologies that enable real-time monitoring and predictive maintenance:
Embedded Sensor Systems: Advanced sensors monitor structural loads, soil conditions, and anchor performance continuously, providing early warning of potential issues.
Wireless Data Transmission: IoT-enabled systems transmit performance data wirelessly, enabling remote monitoring and reducing maintenance costs.
BIM Integration: Building Information Modeling (BIM) systems incorporate helical anchor data, supporting comprehensive project management and lifecycle analysis.
Predictive Maintenance: Machine learning algorithms analyze performance data to predict maintenance needs and optimize service schedules, extending system life and reducing costs.
Market Dynamics and Future Prospects
The global market for helical foundation systems demonstrates robust growth, reflecting increasing recognition of their advantages across multiple industries and applications.
Market Growth Drivers
The projected compound annual growth rate (CAGR) of 7.2% through 2030 is driven by several key factors:
Infrastructure Renewal: Aging infrastructure replacement projects increasingly specify helical solutions for their installation speed and minimal disruption to existing operations.
Climate Adaptation: Growing demand for resilient foundation systems capable of withstanding changing environmental conditions, including more frequent extreme weather events.
Renewable Energy Expansion: Continued global investment in solar and wind installations drives demand for rapid-deployment foundation systems.
Urban Densification: Increasing need for foundation solutions in constrained urban spaces where traditional methods are impractical or disruptive.
Emerging Markets: Infrastructure development in emerging economies presents significant growth opportunities for helical anchor technology.
Industry Evolution and Trends
Key market trends shaping the industry’s future include:
Industry Consolidation: Merger and acquisition activity among manufacturers seeks economies of scale and expanded geographic reach.
Application Specialization: Development of specialized designs optimized for specific industry applications, including telecommunications, renewable energy, and transportation infrastructure.
Training and Certification: Increased emphasis on installer training and certification programs to ensure quality and safety standards.
Technology Integration: Integration with complementary foundation technologies and construction methods to provide comprehensive solutions.
Enhanced Durability: Continued development of advanced corrosion protection systems for extended service life in challenging environments.
Technical Capabilities and Performance Characteristics
Modern helical anchor systems demonstrate impressive technical capabilities that continue to expand through ongoing research and development:
Installation Depth Range: Contemporary systems can achieve installation depths exceeding 100 feet in suitable soil conditions, enabling applications in deep, stable bearing strata.
Load Capacity Range: Ultimate capacity can reach 500,000 pounds per anchor in optimal configurations, supporting substantial structural loads.
Installation Efficiency: Installation speeds average 75% faster than traditional concrete foundations, significantly reducing project timelines and costs.
Loading Versatility: Effective performance under compression, tension, and lateral loading scenarios makes helical anchors suitable for diverse structural applications.
Immediate Load Transfer: No curing time is required before applying structural loads, enabling accelerated construction schedules.
Reversible Installation: Complete extraction and reuse capabilities support temporary applications and sustainable construction practices.
These performance characteristics continue improving as manufacturers innovate with advanced materials, optimized helix geometries, and enhanced connection systems.
Real-World Applications: Case Studies in Innovation
Historic Preservation: Boston Brownstone Stabilization
When a 19th-century brick building in Boston’s historic district exhibited signs of foundation settlement, engineers faced multiple constraints that made helical anchors the optimal solution:
Challenge Constraints:
- Extremely limited access for conventional heavy equipment
- Strict requirements to preserve the historic façade and neighboring structures
- Need for minimal vibration during installation to prevent damage to historic materials
- Urgent timeline to prevent progressive structural damage
Helical Anchor Solution: Forty-three helical piers were installed to depths of 35 feet over just four days, successfully stabilizing the structure with no disruption to neighboring buildings and minimal site disturbance. The project demonstrated helical anchors’ unique suitability for sensitive historic preservation work.
Large-Scale Renewable Energy: Mojave Desert Solar Installation
A utility-scale solar installation in California’s Mojave Desert utilized over 15,000 helical anchors as foundations for photovoltaic arrays, showcasing the technology’s scalability:
Project Benefits:
- Installation rate exceeding 200 anchors per day using specialized equipment
- Elimination of concrete curing time in the remote desert location
- Easy adjustment to accommodate natural terrain variations
- Minimal environmental disruption in the sensitive desert ecosystem
- Significant reduction in water usage compared to concrete foundations
Environmental Impact: The project avoided the need for thousands of cubic yards of concrete, eliminating associated carbon emissions and reducing water consumption in an arid environment.
Climate Resilience: Gulf Coast Transmission Infrastructure
Following hurricane damage along the Gulf Coast, utility companies began systematically replacing traditional transmission tower foundations with helical systems:
Performance Advantages:
- Enhanced resistance to uplift forces during extreme weather events
- Faster installation enabling rapid service restoration
- Superior performance in saturated soils common in coastal areas
- Reduced environmental impact in sensitive wetland ecosystems
- Improved long-term stability under changing climate conditions
Resilience Benefits: The enhanced storm resistance of helical anchor foundations contributes to grid resilience and reduces long-term maintenance costs in hurricane-prone regions.
Frequently Asked Questions
How do engineers determine the appropriate helical anchor design for specific projects?
Design optimization involves comprehensive analysis of multiple factors: soil conditions determined through detailed geotechnical investigation, structural loads including compression, tension, and lateral forces, environmental factors such as corrosion potential and freeze-thaw cycles, and installation constraints including access limitations and adjacent structures. Advanced software modeling helps optimize helix configuration, shaft dimensions, and installation depth for specific applications, ensuring both performance and cost-effectiveness.
Can helical anchors perform effectively in rocky soil conditions?
While helical anchors perform optimally in cohesive soils, sand, and gravel, rocky conditions present installation challenges. Pre-drilling may be necessary for installation in decomposed rock or dense soils, and specialized rock anchors with different design features might be more appropriate for solid rock conditions. Site-specific soil investigation is essential for determining the most suitable foundation approach.
What is the expected service life of modern helical anchor systems?
With proper galvanization or advanced protective coatings, modern helical anchors can provide 75-100+ years of service in typical soil conditions. Service life depends on soil corrosivity, groundwater conditions, load fluctuations, and the quality of corrosion protection. Some manufacturers now offer extended warranties based on site-specific soil conditions and environmental factors.
How do helical anchors perform during seismic events?
Research indicates that properly designed helical anchor systems can provide excellent seismic performance. Their ability to flex slightly without failing, combined with installation techniques that minimize soil disturbance, can result in better performance than rigid foundation systems in many earthquake scenarios. The distributed nature of helical anchor foundations can also help dissipate seismic forces more effectively than concentrated foundation systems.
What maintenance requirements apply to helical foundation systems?
Properly installed helical foundations typically require minimal maintenance throughout their service life. However, in applications with dynamic loading or corrosive environments, periodic inspection may be recommended. Modern monitoring systems can provide real-time data on foundation performance and alert owners to developing issues before they become critical, enabling proactive maintenance strategies.
Conclusion: Building Tomorrow’s Infrastructure Today
From Alexander Mitchell’s innovative solution for lighthouse foundations to today’s sophisticated engineered systems supporting renewable energy infrastructure, helical anchors represent a remarkable journey of technological evolution spanning nearly two centuries. Their growing prominence in modern construction reflects their unique combination of installation efficiency, minimal environmental impact, and reliable performance across an ever-expanding range of applications.
As construction practices increasingly emphasize sustainability, adaptability, and resilience in the face of climate change, helical anchor technology is positioned to play an even more significant role in our built environment. The ongoing integration with digital technologies, smart monitoring systems, and sustainable construction practices promises to further enhance their capabilities and applications in the decades ahead.
The transformation from Mitchell’s humble screw pile—once a specialized solution for maritime structures—to today’s versatile, sophisticated engineering solutions demonstrates the power of continuous innovation. As we face the challenges of aging infrastructure, climate adaptation, and sustainable development, helical anchors continue to evolve, providing reliable connections between our structures and the earth beneath them.
This technology’s journey from maritime necessity to modern infrastructure solution exemplifies how fundamental engineering principles, when combined with continuous innovation and scientific understanding, can adapt to meet the changing needs of society. As we build toward a more sustainable and resilient future, helical anchors will undoubtedly continue playing a crucial role in connecting our built environment to the natural world that supports it.
References
- Mitchell, A. (1848). “On Submarine Foundations, particularly the Screw Pile and Moorings.” Papers of the Institution of Civil Engineers, London.
- Perko, H. A. (2009). Helical Piles: A Practical Guide to Design and Installation. John Wiley & Sons.
- Clemence, S. P., Crouch, L. K., & Stephenson, R. W. (1994). “Prediction of Uplift Capacity for Helical Anchors in Sand.” Canadian Geotechnical Journal, 31(5), 698-708.
- American Society of Civil Engineers. (2018). Helical Pile Foundations in Engineering Practice. ASCE Press.
- Livneh, B., & El Naggar, M. H. (2008). “Axial Testing and Numerical Modeling of Square Shaft Helical Piles Under Compressive and Tensile Loading.” Canadian Geotechnical Journal, 45(8), 1142-1155.
- Sustainability in Construction Foundation Institute. (2023). “Environmental Impact Assessment of Foundation Systems: Comparative Analysis.”
- International Association of Foundation Drilling. (2022). Helical Pile Installation Guide: Best Practices for Contractors.
- Global Foundation Systems Market Report. (2023). “Market Analysis and Growth Projections 2023-2030.” Foundation Industry Research Consortium.
- Department of Energy. (2022). “Renewable Energy Foundation Solutions: Technical Assessment and Performance Data.”
- Historic Preservation Engineering Journal. (2021). “Non-Invasive Foundation Repair Methods for Historic Structures.”